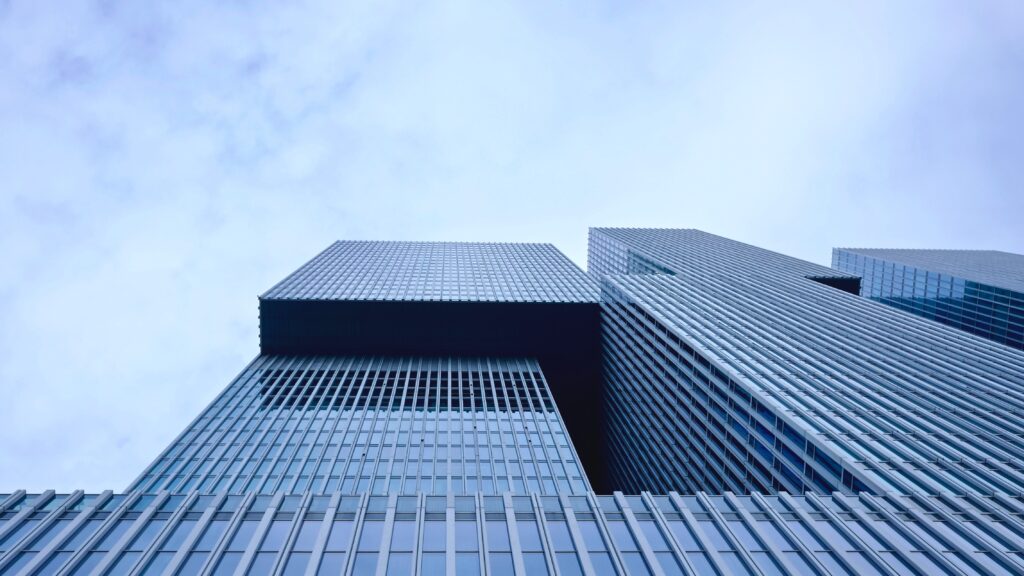
As a Project Architect, your role is broad and demanding. You are responsible for organizing the production effort, aligning documentation with the project schedule, coordinating consultant work, and helping the team meet both project goals and budgets. Throughout Schematic Design, Design Development, and Construction Documents, you are the primary facilitator of the design process, making sure that the evolving documents are aligned with the project’s intent and scope.
Part of managing this process successfully is understanding what to expect from your consultants, especially your MEP/FP team. Mechanical, electrical, plumbing, and fire protection systems touch almost every part of a building, yet they operate in a technical space that many architects aren’t deeply familiar with. While you don’t need to know every calculation or system detail, you do need to know what services they are providing, what deliverables are expected at each phase, and where coordination is most critical.
This article outlines the essential services, deliverables, and coordination expectations for MEP/FP consultants, with the goal of giving architects a clear roadmap for better project planning, stronger consultant integration, and smoother project delivery. (MEP Checklists are provided for download at the end)
2. What Are the Basic Services of an MEP/FP Consultant?
At its core, the role of the MEP consultant is to design the systems that allow a building to function, from keeping occupants comfortable and safe to making sure the lights stay on. Their work spans mechanical, electrical, plumbing, and fire protection design, often in parallel with code compliance, coordination with specialty consultants, and support for utility and agency approvals. These are the core responsibilities, but each consultant may also offer an expanded list of services. That list should be reviewed and agreed to early in the project.
Some of the Basic services typically include:
- HVAC systems: Layouts and equipment sizing for air distribution, ventilation, heating, and cooling. This includes central systems as well as zone-level conditioning, particularly for clinical or equipment-heavy spaces.
- Building automation and controls: Design of temperature regulation and building management systems to monitor and adjust HVAC operation.
- Electrical and fire alarm systems: Design of electrical distribution systems to support lighting, equipment, and specialty loads, including emergency and standby power for life safety systems. Fire alarm design includes notification devices, control panels, and system integration as required by code.
- Plumbing and fire protection systems: Layouts for domestic water, sanitary waste, storm drainage, fire sprinkler, and standpipe systems.
- Lighting support: Design of back-of-house lighting such as mechanical rooms, stairs, and utility areas. While front-of-house lighting is typically handled by a lighting designer, the MEP team ensures power and control infrastructure is in place.
- Telecom and IT conduit planning: Infrastructure routing between points of entry and riser closets. Cabling and equipment design is typically provided by others.
- Support for third-party systems: While MEPs do not design AV, security, or food service systems, they provide the utilities, power, and ventilation required to support them, provided those requirements are shared early.
- Energy code compliance: Verification that the systems designed meet local, state and national code requirements for energy use, in coordination with the architect, lighting designer, energy modeler, and sustainability team.
The services outlined here represent a typical foundation of the MEP/FP consultant’s role, although specific project needs and goals may require tailoring or expansion. While certain responsibilities like lighting design, LEED consulting, or telecom layouts often fall to other team members, the MEP consultant is responsible for ensuring those systems can be powered, cooled, and integrated into the overall building infrastructure.
3. What Are Not Considered Basic Services by an MEP Consultant?
While MEP/FP consultants cover a broad range of essential services, some tasks fall outside their standard scope and are considered additional or excluded. Clarifying these early helps with budgeting and can also help set expectations for project scope and consultant responsibilities.
Additional Services:
These are just a few examples. Typically, the MEP engineering firm will provide a more comprehensive list of additional services that should be reviewed and agreed to as part of the consultant’s contract.
- Commissioning Services: Participating in system testing, reviewing the commissioning agent’s plans and procedures, would be considered an add service.
- Energy Modeling and Sustainability Consulting: Life-cycle cost studies, carbon threshold analysis, and repeated model iterations tied to incentive programs are typically considered additional services.
- Advanced Fire Protection Analysis: Specialized design beyond basic code compliance, including smoke control strategies for complex spaces like large atriums, underground structures, or high-rise buildings.
- Building Information Modeling (BIM) Beyond Standard Levels and Digital Twin Integration: While basic BIM coordination is standard, more advanced outputs such as LOD 350 models, or integration with digital twin platforms may be considered additional services.
Excluded Services:
These services are generally outside the MEP consultant’s responsibilities:
- Architectural Lighting Design: Front-of-house lighting, particularly aesthetic and specialty systems, is typically handled by a dedicated lighting designer. The MEP consultant generally provides power and control infrastructure to support these systems.
- Air Entrainment or Re-entrainment Modeling: Modeling to assess the recirculation or intake of exhaust air, especially in complex healthcare or lab environments, is typically outside standard scope and may require a specialist.
- Post-Occupancy Evaluations: Assessments conducted after building occupancy to evaluate system performance are often considered separate services.
Recognizing these boundaries helps clarify responsibilities and reduces confusion as the project progresses.
4. What Are the MEP Deliverables by Phase?
The design deliverables provided by the MEP/FP consultant are closely tied to each phase of the project and serve multiple purposes. In addition to documenting design intent and technical coordination, these early-phase outputs are often used to support cost estimates and schedule planning. Developing system criteria, load assumptions, and early layouts provides critical input to quantity takeoffs, pricing efforts, and construction phasing. In early phases, this effort is often led by the architect and estimator if a construction manager has not yet been engaged.
Basis of Design
The Basis of Design is one of the earliest technical deliverables produced by the MEP consultant. It documents the initial design criteria and performance targets for each system, such as HVAC zoning, ventilation requirements, electrical demand, and plumbing capacities. These criteria are shaped through early discussions with the architect, planning team, and end users. The BOD outlines assumptions and system approaches based on the building program and is updated as design progresses. It sets the foundation for how systems are configured, sized, and evaluated throughout the remainder of the project.
Concept Planning and Massing
Alongside the development of the BOD, MEP consultants begin shaping the building’s technical layout. This includes identifying major mechanical and electrical equipment locations, riser paths, shaft sizes, and utility points of entry. As part of this effort, they also provide preliminary equipment weights to the structural engineer to support early structural planning and coordination. Their input influences floor-to-floor heights, zoning of program areas, and the placement of critical infrastructure. These early studies help the design team coordinate the architectural massing with technical constraints and anticipate future spatial conflicts.
On projects with accelerated schedules, certain infrastructure elements may need to be documented earlier than others to support phased work or procurement planning. In these cases, the MEP/FP consultant assists by identifying and detailing items such as utility entry points, shaft space, or major equipment zones that could impact the early construction sequence.
Schematic Design
The Schematic Design phase marks the transition from conceptual strategy to preliminary system planning. For the MEP/FP consultant, this phase focuses on converting the performance targets outlined in the Basis of Design into a coordinated approach for system layouts, space allocation, and early integration with architectural planning.
- Outline specifications and system narratives that define proposed system types, design criteria, insulation standards, and performance assumptions. that outline the systems being considered and their general configuration.
- Preliminary system layouts that support coordination with structure, architectural layouts, and ceiling zones, and allow for early design pricing.
- Preliminary riser diagrams for mechanical, electrical, plumbing, and fire protection systems to define early routing strategies, shaft allocations, and vertical coordination assumptions.
- Initial equipment weights provided to the structural engineer to assist with early load assessments.
- Defined spatial requirements for mechanical rooms, risers, vertical distribution, and utility entrances.
- Preliminary energy model inputs based on early performance assumptions, including ventilation, thermal loads, and sound levels. based on early system assumptions.
- Coordination with utility companies and preparation of utility load letters.
- System sizing assumptions shared with the project team to support estimating and interdisciplinary design development.
When early or phased packages are needed, such as foundations or utility rough-ins, the MEP/FP consultant supports by identifying and documenting utility entry points, shaft reservations, and major mechanical elements that could impact early construction. While final system selections may not yet be made, the schematic phase ensures there is enough clarity to move into more detailed design work.
Design Development
By the Design Development phase, the MEP/FP consultant’s focus shifts to refining the initial concepts into coordinated, spatially-resolved systems that align with the architectural and structural plans. System diagrams are expanded, layout conflicts are resolved, and performance assumptions are validated. Design Development documents form the foundation for estimating, permitting, and the coordination of long-lead equipment.
Key efforts during this phase typically include:
- System refinement and coordination: Update major system layouts and begin resolving horizontal and vertical routing paths. Coordinate closely with structure to verify clearances, penetrations, and load requirements.
- Room and equipment planning: Define mechanical, electrical, and plumbing room layouts. Document the footprint, height, and clearance zones for major equipment.
- Energy and load development: Continue developing detailed load calculations and energy model inputs. Reconfirm energy code requirements and system performance targets including acoustics, ventilation rates, and equipment sound levels. Adjust system sizing as the architectural layout evolves.
- MEP riser and distribution diagrams: Advance riser diagrams and routing plans to coordinate with structure, ceiling zones, and interstitial space. Confirm horizontal and vertical system clearances across disciplines.
- Lighting and power layouts: Develop typical floor plans for electrical and lighting distribution. Coordinate with the lighting designer on scope and control strategies.
- Agency coordination: Assist with early filing packages, including outline specifications or stamped drawings as required.
- Cost and procurement alignment: Participate in cost reviews, respond to value engineering requests, and assist with early bid or prepurchase packages.
By the end of Design Development, the documents should be technically and graphically developed to support early bid packages, quantity takeoffs, and agency or owner approvals. Coordination should be advanced enough to minimize major design shifts moving into the CD phase.
Construction Documents
The Construction Documents (CD) phase builds upon the development and coordination completed during Design Development. At this stage, the MEP/FP consultant finalizes system layouts, performance criteria, and equipment selections to produce fully detailed drawings and specifications suitable for bidding, permitting, and construction. These deliverables must incorporate any approved value engineering changes from previous phases.
Key deliverables during this phase typically include:
- Finalized MEP/FP drawings and specifications that fully describe mechanical, electrical, plumbing, and fire protection systems for construction and code compliance.
- Coordination with all design consultants to confirm alignment of all systems, slab penetrations, ceiling routing, and cross-disciplinary design requirements.
- Power and equipment coordination with electrical device layouts and connection requirements provided by the architect or equipment planners.
- Agency and filing documentation prepared and signed as required by the authority having jurisdiction. This includes sealed drawings to support permit applications.
- Support for LEED documentation in collaboration with the sustainability consultant to ensure MEP/FP systems are reflected in the final submission.
- Phased document issues as required by the project work plan, including preliminary CDs, bid sets, and 100% construction issue drawings.
CD phase deliverables ensure that all scope is properly defined and documented for procurement and construction. These documents also form the basis for regulatory review and are used to support and finalize ongoing bid packages and long-lead procurement that were initiated in earlier phases.
5. What Information Is Required by the MEP Consultant?
During the Schematic Design phase, the MEP/FP consultant relies on coordinated input from the architect, client, and other consultants to initiate early system planning. While all design elements remain preliminary at this stage, timely access to foundational information is essential for producing documents that support massing, layout coordination, and cost estimating.
Typical categories of information needed at this phase include:
- Architectural backgrounds and program layouts
- Preliminary floor plans showing space types, gross square footages, and core locations
- Defined program elements such as assembly spaces, residential units, support rooms, or back-of-house areas
- Draft ceiling zones and floor-to-floor heights for coordination of ductwork, piping, and structure
- Building envelope and site design criteria
- Early façade performance values (e.g., U-values, SHGC, visible light transmittance)
- Preliminary glazing and cladding types
- Louver locations, intake/exhaust areas, and other envelope penetrations
- Vertical and utility coordination
- Shaft and riser assumptions for routing mechanical, electrical, and plumbing systems
- Location and requirements for major equipment rooms and vertical distribution zones
- Utility entry points and civil coordination for water, storm, sanitary, gas, and electric service
- Preliminary specialty systems and equipment inputs
- Owner-furnished equipment or specialized systems with known utility or ventilation needs
- Preliminary locations for elevators, AV, security, lighting control panels, and fire command centers
- Structural coordination
- Column grids, slab thicknesses, and framing concepts
- Known transfer structures or mechanical trusses impacting vertical routing
Providing this information in a timely and organized way enables the MEP/FP consultant to size systems appropriately and integrate their work into the larger design narrative. As the project progresses, assumptions made at this stage are refined, but solid baseline input reduces redesign risk and keeps the team aligned.
Design Development Information Requirements
As the design becomes more defined during the Design Development phase, the MEP/FP consultant requires more specific and coordinated inputs to continue developing system layouts, resolving conflicts, and preparing for construction-level documentation. This phase also sets the foundation for cost estimating, agency review, and early procurement planning.
Information needs at this stage typically include:
- Acoustical design criteria related to equipment noise limits, sound-sensitive spaces, and zoning strategies that influence ventilation and equipment layout decisions.
- Finalized architectural backgrounds with structural grid, wall types, floor-to-floor heights, and ceiling conditions.
- Confirmed locations of rated walls and partitions to coordinate damper types, penetrations, and fire-stopping requirements.
- Updated envelope design criteria including window and wall assemblies, insulation values, shading strategies, and roof performance data to inform mechanical sizing and energy modeling.
- Reflected ceiling plans and lighting layouts, including fixture locations, zoning, and control strategies,especially in large assembly, performance, or public-facing areas.
- Exit and egress signage coordination for integration of emergency lighting and power.
- Elevator layouts and preliminary mechanical/electrical interface details, such as machine room size, shaft location, and motor sizing.
- Utility and site requirements for final placement of service entry points, meter rooms, and any requirements driven by site landscaping or hardscaping.
- Specialty system coordination for AV, food service, digital signage, and low-voltage or smart building infrastructure. This includes panel locations, power/communications requirements, and relevant heat or ventilation loads.
- Equipment data and cut sheets from owner-provided or third-party systems (e.g., vendor-furnished equipment for performance spaces, educational labs, or terminal infrastructure).
- Mechanical criteria for large open or complex zones, including ceiling height coordination, air distribution strategy, diffuser types, and exhaust requirements.
Early access to this level of detail reduces redesign risk and supports the development of more complete documents, particularly when fast-track or early bid packages are required.
Construction Document Information Requirements
By the Construction Document phase, most design assumptions should be resolved and fully coordinated inputs are required to support the completion of detailed MEP/FP documentation. At this stage, the focus shifts to finalizing system layouts, verifying equipment infrastructure, and producing information suitable for bidding, filing, and construction.
Typical information requirements include:
- Final architectural and structural backgrounds in Revit format to support coordinated documentation and modeling.
- Confirmed locations of all rated walls and fire/smoke partitions, with damper coordination and penetrations identified.
- Detailed building envelope performance including glazing ratios, U-values, wind loads, and roof performance metrics.
- Reflected ceiling plans and fixture layouts showing all lighting, sensors, and ceiling-mounted equipment with zoning and control intent.
- Final lighting and power coordination, including lighting density data, emergency egress lighting, and system integration points.
- Elevator layout and equipment loads, including machine room sizes, shaft locations, and motor sizing, with updates to power and HVAC connections.
- Roof system requirements including drain locations, landscaping provisions, davit points, and service zones for mechanical or electrical equipment.
- Specialty system confirmation for AV, food service, digital signage, and low-voltage packages. Final power, cooling, or integration requirements must be issued.
- Equipment cut sheets and infrastructure coordination for all items requiring MEP connections, including owner-furnished equipment.
- IT and device locations, including server rooms, AV hubs, and workstation-level power/data coordination.
- Final air and exhaust system zoning, including diffuser types, acoustic separation, smoke control strategies, and pressurization requirements.
- Agency and filing coordination for any documentation that must be sealed or formatted for AHJ submissions.
To complete the deliverables outlined in their scope of work, the MEP/FP consultant depends on receiving well-organized and timely information throughout the Construction Document phase. This information must be coordinated across all disciplines and delivered in alignment with the project schedule to support documentation milestones and maintain delivery commitments.
6. Early Deliverables and Fast-Track Package Strategy
On projects with aggressive schedules or phased construction sequencing, early MEP/FP deliverables often support enabling work, regulatory submissions, or early procurement. These fast-track packages require careful planning and coordination to ensure design information is available in time to meet milestone dates.
Typical examples include:
- Site Package: This early-phase deliverable identifies all required utility service connections, relocations, and upgrades. It must be closely coordinated with the civil engineer, site design team, and utility authorities to align with construction phasing and permitting schedules.
- Early Foundations Package: Developed to support early permitting and structural approvals, this package includes the layout and coordination of below-grade MEP/FP scope. It typically covers storm and sanitary drainage, foundation wall penetrations, and electrical grounding systems that must be in place before foundation work proceeds.
- Infrastructure Package: Focused on major building systems that influence structural or vertical layout, this package includes risers, utility shafts, and core routing requirements. It also includes prepurchase specifications for long-lead items such as switchgear, air handling units, and central plant equipment when required for procurement planning.
The timing of these packages must be coordinated across all disciplines. Input from the architect, structural engineer, and other specialty consultants is necessary to define scope, resolve space conflicts, and identify integration requirements. Typically, the construction manager identifies which systems need to be advanced to meet project milestones, with input from the design team. The MEP/FP consultant supports this effort by providing the necessary technical information and coordinating with the project manager or construction manager to align system readiness with the construction sequence.
7. BIM Practices and Expectations
The MEP/FP consultant is expected to develop all design documentation within a Building Information Modeling (BIM) platform, with Revit as the standard software environment for modeling and coordination. BIM is central to communicating design intent, resolving spatial conflicts, and ensuring cross-disciplinary alignment throughout the life of the project.
All major MEP/FP systems, including HVAC, electrical distribution, plumbing, fire protection, and infrastructure support for IT, AV, and security, must be modeled in Revit and coordinated with the architectural and structural models. The BIM model serves as the primary coordination tool and must reflect the level of detail required by each design phase.
Standard BIM expectations include:
- Discipline Ownership with Cross-Discipline Review: Each discipline within the MEP/FP team is responsible for maintaining its own model components. However, the consultant is also expected to self-perform cross-checks across mechanical, electrical, and plumbing systems for internal coordination. It is not the architect’s responsibility to identify conflicts between MEP systems.
- Model Progression and Level of Development (LOD): Model detail should align with the design phase:
- LOD 100 (SD phase): Conceptual massing and system zoning
- LOD 200 (DD phase): Approximate geometry, routing assumptions, and system relationships
- LOD 300 (CD phase): Detailed geometry, layout accuracy, and basic fabrication intent Design models are typically not developed beyond LOD 300 unless specifically requested for fabrication or construction coordination.
- Clash Detection and Spatial Resolution: During DD and CD phases, the MEP/FP team is expected to participate in structured coordination reviews using Navisworks or other clash detection platforms. All system conflicts must be resolved digitally in the model, including ceiling congestion, structural penetrations, and access clearances.
- Modeling Standards and Sharing Protocols: Revit files must follow project standards, including shared coordinates, view templates, file-naming conventions, and linked model hierarchies. Regular uploads to the shared model environment are required to maintain alignment across disciplines.
- Model Scope Boundaries: While large-diameter piping, major ductwork, conduit banks, and equipment must be modeled, elements such as piping under 2 inches in diameter may be excluded unless explicitly required. The model should support coordination, not replicate fabrication-level detailing.
Clear modeling responsibilities and milestone coordination dates should be defined in the project’s BIM Execution Plan (BxP). This ensures all consultants are working from the same expectations and that deliverables are complete, clash-resolved, and ready to support estimating, review, and construction documentation.
8. Quality Control and Coordination
No deliverable should be considered complete unless it has gone through a careful and deliberate internal quality control process. This isn’t something that begins at the end of a phase. Good QA/QC is integrated into the workflow from the very beginning and continues throughout every stage of the project. For MEP/FP consultants, that means system layouts are coordinated internally, documentation is checked regularly, and the model and drawings align with both the building’s design intent and construction feasibility.
Consultants should have a written QA/QC plan for each project and share it with the architect. The expectation is that this plan builds on lessons learned from past projects and is tailored to address common issues before they become problems in the field. These reviews must go beyond simple checklists—they require design judgment and a strong understanding of the architectural layout and structural framework.
While every project is different, certain coordination issues come up repeatedly:
- Ceiling plenum congestion: Ceiling space is often one of the most contested zones in the building. Every duct, pipe, conduit, sprinkler line, and lighting fixture is trying to fit into a space that’s already constrained by structure. All systems must be modeled, with clear routing and elevation alignment.
- Coordination with structural systems: Shaft openings, beam penetrations, and slab thicknesses must be confirmed early. MEP consultants should never assume uninterrupted routing.
- Misalignment with lighting, coves, and finishes: Ducts and conduit must not conflict with lighting layouts or integrated ceiling details. Coordinating these conditions is critical, especially in public or high-finish areas.
- Missing dampers and smoke control coordination: Wall and partition ratings need to be confirmed to determine where smoke, fire, or combination dampers are required. These often get overlooked if wall types aren’t shared in time.
- Access requirements and equipment clearance: Every piece of mechanical and electrical equipment has a required service clearance. QA/QC should include confirmation of these zones as well as walkable access paths, and any support platforms or catwalks.
- Equipment and feeder sizing: Undersized ductwork, piping, or power feeders can result from coordination oversights or outdated assumptions. QA/QC review should confirm that sizing reflects the most current design loads.
- Humidity and environmental conditions: Special environmental conditions, such as precise temperature and RH ranges in museums, performance spaces, or healthcare buildings must be confirmed early and incorporated into the mechanical system design.
Ultimately, the MEP/FP consultant is responsible for checking their own work, including coordination between trades within their own scope. That said, the architect must also review the consultant’s documents to ensure alignment with the architectural design, structural systems, and overall project goals. Coordination is a shared effort and essential for delivering a well-integrated set of documents. Quality control isn’t just about avoiding errors, it’s about delivering a complete and coordinated set of documents that allows the project to move forward smoothly into construction.
9. Sustainability and Energy Performance
The MEP/FP consultant plays a central role in achieving high-performance building goals. While compliance with local energy codes is a baseline requirement, the consultant’s contributions should go further, supporting the building’s energy performance, carbon reduction goals, and long-term operational efficiency.
MEP systems are responsible for the majority of a building’s energy use. Mechanical equipment selection, electrical load management, ventilation strategies, and control systems all directly impact the building’s energy footprint. As the industry shifts toward all-electric and low-carbon buildings, the MEP consultant’s decisions have greater implications than ever before.
During design, the MEP consultant is expected to:
- Develop systems that meet or, better yet, exceed minimum code requirements for energy efficiency
- Recommend high-performing, Energy Star rated equipment with lower operational energy use.
- Coordinate early with the architect, façade consultant, and lighting designer to ensure inputs required for energy modeling are complete
- Perform energy compliance modeling and provide the associated mechanical and electrical documentation required for code submissions
- Support energy modeling efforts for sustainability certifications such as LEED, focusing on Minimum Energy Performance and Optimize Energy Performance credits where required
- Prepare and issue a building energy modeling report that demonstrates energy code compliance and outlines overall building performance relative to project sustainability goals
MEP consultants are in a critical position to shape building energy performance and operational carbon outcomes. Their system design choices have long-term impacts on building efficiency, flexibility, and environmental performance. Although sustainability consultants often guide broader certification efforts, it is the MEP/FP consultant’s technical decisions that directly influence how well a building meets its energy and carbon goals.
10. Final Thoughts
The MEP/FP consultant is one of the architect’s closest allies throughout the development of a project. From the earliest planning stages through construction completion, their technical expertise in mechanical, electrical, plumbing, and fire protection systems is critical to realizing a fully functional, coordinated, and high-performing building.
As architects, we are not expected to know every detail about system design, load calculations, or code compliance modeling. However, understanding the general scope of MEP/FP responsibilities and knowing what to expect in terms of deliverables is vital to managing the project successfully. Clear expectations, strong coordination, and an integrated design process all depend on recognizing where these disciplines intersect and how they shape the overall project plan.
Good MEP/FP coordination does not happen by accident. It requires active collaboration, clear communication, and a shared understanding of the project’s goals, from basic code compliance to more ambitious targets like net-zero energy use, operational carbon reduction, and resilient infrastructure.
Ultimately, a well-organized and proactive relationship with the MEP/FP consultant strengthens the architectural vision, improves project delivery, and enhances building performance for the long term.
BE the ONE
Downloads: Design Phase Checklists
- MECHANICAL (HVAC):
- PLUMBING (PL):
- FIRE PROTECTION (FP):
- FIRE ALARM (FA)
- ELECTRICAL (ELEC)